Brass
Brass is an alloy made of copper and zinc. The properties of brass can be substantially modified by changing the Cu/Zn ratio. The "Encyclopedia of Materials and Finishes" writes: "Most of the brasses are within the alpha field of the phase diagrams, thus maintaining good cold-working properties. With higher zinc content of about 40%, the beta phase facilitates hot working. The addition of zinc decreases the melting point, density, electrical and thermal conductivities, and modulus of elasticity."(page 177)
For a copper content more than 61% the structure is homogeneous. It consists of alpha brass which is rather ductile. If the amount of zinc is more than 39% the structure consists of both alpha brasses and beta brasses. Beta brasses crystals are more brittle. The most common ratio are as follows:
Alpha brasses Copper: >65%, Zinc <35%
Alpha or cold working brasses contain up to 37% zinc. They can be bent and deep drawn at low temperature. Lower zinc contents, between 5-20%, resemble gold in its color. They are particularily used for jewellery and decorative purpose.
Alpha-beta brasses Copper 60%, Zinc 38-42%
Alpha-beta brasses is known as hot working brasses. Their deformation capabilities at room temperature are poor. On the other hand it can be extruded into very complex sections at higher temperatures. The hot forging process of these brasses in closed dies is known as hot stamping.
Beta brasses Copper 50-55%, Zinc 45-50%
Beta brasses are used for castings, it is harder and stronger than alpha brasses.
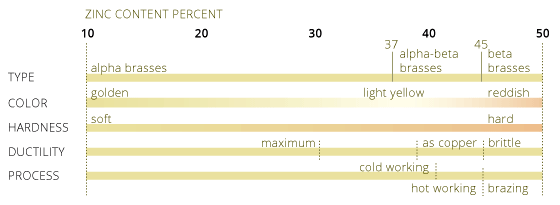
Following some common brass alloys with their chemical compositions and use.
Admiralty brass Zinc 30%, Tin 1%
used to inhibit dezincification.
Aich's alloy Zinc 36.58%, Tin 1.02%, Iron 1.74%
Designed for use in marine environment because of its corrosion resistance. Its appearance resembles that of gold. The addition of iron hardens the alloy and makes it more suitable for forging. It was patented by J. Aich in 1860.
Aluminuim brass Zinc 22%, Aluminium 2%
Due to the aluminium content there is a improving corrosion resistance. It is used for marine works.
Arsenical brass Zinc 30%, Arsenic 0.02-0.06%
It is mainly used for heat-exchanger, boiler fireboxes.
Brazing brass Zinc 25%
Used for drawing, spinning, springs etc.
Cartridge brass Zinc 30%
It has the highest ductility in the yellow brass series. It is used for ammunition cartridge cases, watch parts, electrical connectors, radiator tubes and much more.
Common brass Zinc 37%
The standard for cold working.
Gilding metal Zinc ~5%
The softest kind of brass and typically used for bullet jackets, it is used for coins and medals too.
High brass Zinc 34%
It has a high tensile strength and is used for stamping, drawing, and blanking operations. Common products are: springs, screws, rivets and chains.
Leaded brass Lead 0.5-3.5%
The component lead promotes machinability. It is used for keys, gears, valve parts, screws, clock parts etc.
Manganese brass Zinc 38%, Manganese 1.0%, Iron 1.0%
The manganese improves castability of the alloy. It is used for valves, cylinder, nuts and bolts, hydraulic components and marine components.
Nickel brass Zinc 24.5%, Nickel 5.5%
It is used to make pound coins in the pound sterling currency.
Nordic gold Zinc 5%, Aluminium 5%, Tin 1%
Used in 10, 20, and 50 cent euro coins.
White brass Zinc 45%
The malleability of brass depends on the zinc content. White brasses are called those brasses containing more than 45 percent zinc. Such brasses are of little industrial importance. A granulated form ist used in brazing (soldering).