Coil Coating Systems
Liquid Paints
Liquid paints are mainly used for the coating process of prepainted metal and comprise some principal ingredients: resin (binders), pigments, solvents and additives. During the curing process the solvent evaporates and leaves the pigments surrounded with resin glued on the substrate. The solvent is not incorporated into the finished product. Before the solvent is dried, the pigments are homogeneously distributed on the metal surface. The resin holds the pigment particles and protects them from environmental influences and pollutants (including UV radiation and industrial pollution).
There are two types of pigments available: organic and inorganic. The inorganic pigments are basicially the same as they were used for making porcelain. They are manufactured from various metal oxides by various costs. In essence, they all are considered premium products with enormous colour stability and a very good resistance against chemical agents. Unfortunately not all colours are available for metal oxide and commonly they are blended with organic pigments.
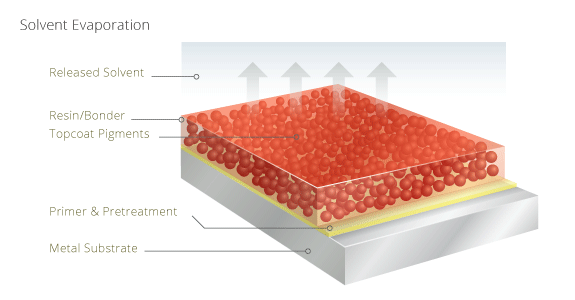
and the colour pigments remain surrounded and protected by the resin/bonder.
Copyright © 2025 build-your-vision.eu; without any guarantee or liability
In general when a liquid paint coating is called
- Acrylic
- Epoxy
- Polyester
- Plastisol (PVC)
- Polyurethane
- Polyvinylidene flouride (PVDF)
it refers to the polymeric resin. In the industrial coating process resins are blended from several ingredients (additives) in order to achieve specific coating properties like gloss, or resistance against mechanical influences. Some additives are included to optimize the production process.
After the pretreatment of the steel sheet, primer and topcoat are applied. This two-coat system (primer and top-coat) is widely used for the commercial cladding industry. Of course there are highly differentiated coated products available with more than two layers. Almost any product requirement regarding corrosion protection, flexibility or final visual appearance can be achieved in an even more complex and highly controlled coil coating process with liquid paints.
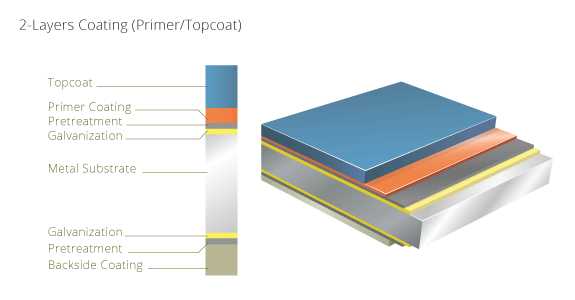
Copyright © 2025 build-your-vision.eu
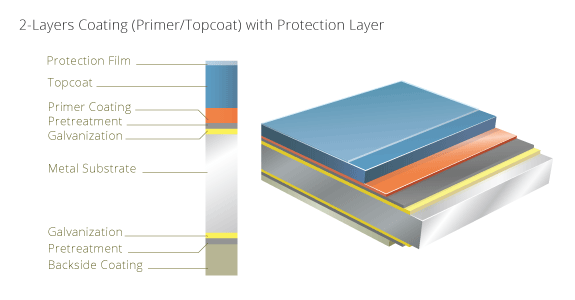
Copyright © 2025 build-your-vision.eu
In Figures 1-2 the reverse side of the substrate has a zinc layer, a pretreatment layer, and a protective layer coat. For many applications only one side of the strip is exposed to weather and environmental conditions and abrasion. Therefore only one side needs to be covered with a strong protective coating layer system. The backside is significantly less exposed and usually protected with only one layer of liquid paint. The final application of the coated strip demands enormous flexibility for every single part of the coil coating process. In the construction industry for the backside coating it may also be required to ensure good adhesion of foams as insulation.
There a many more coating concept available even with more than 2-layers. In this case usually the already coated metal strip has to pass throught the coating line twice.
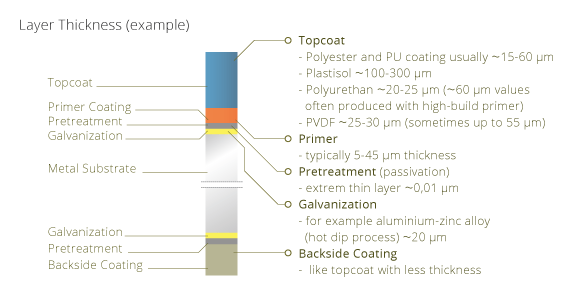
leading to different results accordingly to customer requirements.
Copyright © 2025 build-your-vision.eu; without any guarantee or liability
Polyester coatings are cost-efficient solutions and widely used in the construction industry. The modifiability of the formular allow flexible results such as very hard and tough and on the other hand very mouldable including a very good resistance against scratches.
Polyurethane (PU) coatings improve material properties like durability, adhesion and resistance. They are cross-linked with other compounds to the substrate which leads to higher material costs. Polyurethane coatings are considered outstanding suitable for household appliances.
Plastisols coatings are based on PVC. With an increasing layer thickness up to 150 to 200 µm they offer very good substrate protection even in aggressive industrial atmosphere. Plastisol coating have been used as a standard in the construction industry for building envelope and weather exposed industrial components.
Polyvinylidene fluoride PVDF coatings exists more than 30 years and offer still the highest resistance against UV radiation and other weather influences. Combined with its excellent formability and durability PVDF coatings play a major role in demanding architectural applications.
Laminated Films
Another widely used coil coating method is the protection of the metal substrate with laminated films. Those stand-alone film products can be modified easily and as a result a wide variety of laminates exists in many different colours, gloss degrees or with embossed textures. With the same flexibility for the visual appearance and decor all aspects of the film resistance functions were investigated. Some film products have an enormous resistance against chemical agents and/or abrasion others against weather exposure like sun, rain or heat. In the fields of appliances, furniture, clean-rooms and ship-building, laminated film protected metal strips are the preferred solution.
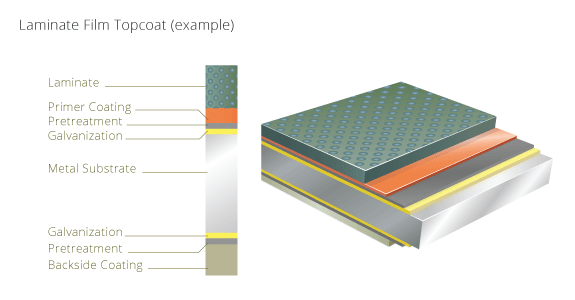
Sometimes the laminate is directly molten on the substrate.
Copyright © 2025 build-your-vision.eu; without any guarantee or liability
Laminated film products are typically bonded through a molten glue layer between the laminate and the metal substrate. Some laminates are thermally laminated onto a preheated strip in a continuous process without an adhesive layer. The film melts onto the strip.
The main chemical types of laminate are:
- Polyvinyl chloride (PVC)
- Polyvinyl flouride
- Polypropylene (PP)
- Thermoplastic acrylics
- Polyethylene terephthalate (PET)
PVC and PET laminates are also used as food safe (FDS) protective layer. Due to higher scratch resistance and a better corrosion protection than most lacquer systems laminated metal products have been particularly established for some applications including: aerosol cans, easy open ends for food cans, components for containers of water based products.
Laminate film products exist in uncountable designs from wood-like, stone-like, or any other individual printed picture to embossed designs making images appear more realistic or to achieve more abstract effects. There are almost no limitations and this might be one of the reasons that especially in the furniture industry laminated metal sheets are quite prevalent.
Powder Coating
Powder coatings for continuous coil coating lines has been developed and improved for the need and wish to establish a solvent-free and therefor a more environment-friendly coating process. Powder coating is sometimes referred as "dry paint". Powder coating is widely used for fabricated steel parts like bicycle frames, handrails, fences, and individual fabricated steel frames.
The primary benefit of powder paint is the 100% use of the paint particles. The particles are electrical charged and then sprayed on the grounded substrate, so the powder is strongly attracted to it. After applied to the substrate, it is then heated by some kinds of oven (gas, electric, infrared) until the particles are melt and fused into a solid paint film. From an economic point of view powder coating seems to suffer from limitations in speed and the flexibility to make thin coats.
On the other hand during the drying process of liquid paints solvents are released to the environment. On www.powdercoil.com it is mentioned: "These solvents are called VOC’s (volatile organic compounds), i.e., acetone, benzene, dichloromethane, ethanol, methanol, and toluene. Solvents serve as carriers to allow the paint to flow, homogenize and dry. It’s in the drying process that solvents separate from the solids. The solvents must be contained and controlled such that less than 1% can escape to the atmosphere. Capture, control and containment of 99+% of solvent vapors is a very costly and environmentally problematic issue." (as of April 2016).
On www.pcimag.com there is more future-oriented article describing the status of the dry-paint development for coil coatings: "The main advantage of [liquid] coil coating are its fast cure time - approximately 25 seconds - and its ability to create an already-painted substrate that is flexible enough to fabricate parts." and later "... During testing, the powder coil coating achieved a complete cure within 3 to 20 seconds. This cure behavior is substantially different from conventional powder coatings, which typically require cure times of 10-15 minutes at temperatures of 150 to 200°C." (as of April 2016). Furthmore it is stated that strong improvements were done to achieve thinner films and better viscosity. The text summarize the situation that with this novel powder coil coating "metal finishers have a new option for meeting environment regulations and improving productivity, without compromising quality." Unfortunately the source www.pcimag.com does not offer vivid examples about installation and running such coating lines.
Despite the obvious differences of opinion, the present state of the powder coil coating development seems to be promising. Most articles consider it non-competitive to liquid paints, it is a niche in the coil coating industry. Likewise it is considered an economical alternative if special surface textures are desired like "orange peel". It seems that it would be an enormous innovation making the process of powder coating reliable and competitive available for high-performance coil-coating.
An interesting publication about continuous powder coating for coils is published from the "Fraunhofer-Institute" describing a new process named "TransApp". The transfer of the powder is based on the fluidised bed principle in conjunction with high-performance infrared radiators. Direct link: www.fraunhofer.de/documents/N-120600.html