Galvanization (Metallic Coatings)
Corrosion protection for iron and steel is commonly achieved through a metallic coating of the steel substrate. Zinc offers characteristics which makes it one of the preferred metallic coatings available. On wikipedia the three important protective properties of zinc are described as follows: " a) It forms a coating of corrosion-resistant zinc which prevents corrosive substances from reaching the more delicate part of the metal. b) The zinc serves as a sacrificial anode so that even if the coating is scratched, the exposed steel will still be protected by the remaining zinc. c) The zinc protects its base metal by corroding before iron, for better results application of chromates over zinc is also seen as an industrial trend." (source: wikipedia).
During the galvanizing process a layer of zinc or a zinc alloy like zinc-aluminium, zinc-silicon, zinc-aluminium-magnesium etc. is applied to the steel substrate so that the steel itself is completely covered and no longer directly exposed to the environment. Today almost everywhere in building, construction, technical applications, tanks, all kind of coverings, in the domestic appliance sector (white and brown goods) the underlying steel is protected by a metallic coat.
The galvanized steel shows sometimes crystallites known as "spangle". By varying the galvanizing parameters (drying and cooling) the size of the spangles can be adjusted from an apparently uniform surface (almost no visible spangles) to grains with several centimeter.
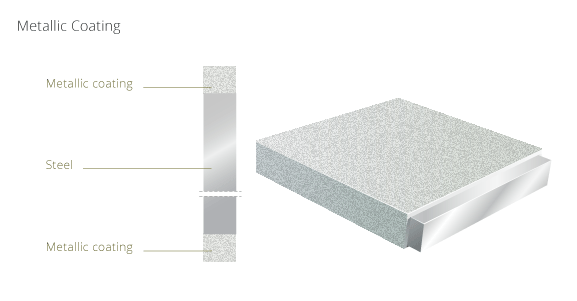
Copyright © 2025 build-your-vision.eu; without any guarantee or liability
In fact the figure above has a misleading approach about the relationship between the zinc/zinc-alloy layer thickness and the size of the metal substrate. Hot-dip galvanized layers for example have a common thickness of between 25-90 µm (10 µm = 0,01 mm; 100 µm is similar to the diameter of a human hair). Compared to the thickness of a thin steel strip with approximately 0,5-0,75 mm the zinc/zinc-alloy layer has only 1/50 to 1/75 thickness of the substrate.
The zinc/zinc-alloy layer itself is divided in several smaller layers with different zinc concentrations.
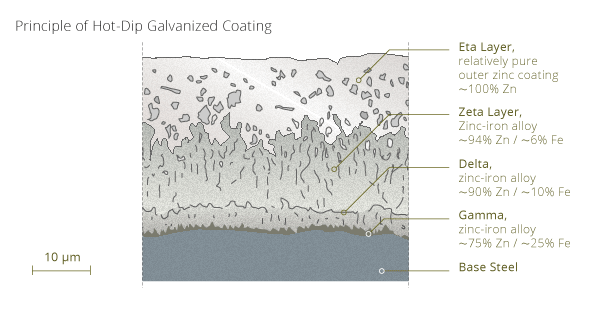
Additional there is an extremely thin oxidized top layer on the outside (Eta) zinc layer.
Copyright © 2025 build-your-vision.eu; without any guarantee or liability
The final metallographic micrograph struture of a galvanized coating depends on the used process and the zinc-alloy. There are several types of industrial galvanizing processes available. Each has unique characteristics and the protective results regarding corners, edges, the thickness of the layer, and densitiy of the coating vary greatly.
Major commercial types of zinc coatings are:
- Hot-dip galvanizing
- Electrogalvanizing
- Galvannealing
- Zinc plating
- Sherardizing (dry galvanization, varporization)
Hot-dip Galvanizing
Hot-dip galvanizing involves the immersing of the steel component into a bath of molten zinc. The zinc bath is heated at about 450°C. The single stages for batch hot-dip galvanizing are:
- Degreasing
- Pickling (chemical cleaning)
- Rinse
- Fluxing
- Drying and heating
- Zinc bath
- Water quench
After immersing fabricated steel structures or steel components into the (7) molten zinc bath it creates a metallurgical bonded layer to the substrate. This cathodic protection against cossorion is self-repairing. The most critical steps to achieve perfect results are the preparation of the surface. The molten zinc will not bond properly to the steel if the surface is not completely clean.
Preparation: during the (1) caustic cleaning (degreasing) surface dirt, grease and oil is removed from the surface. This is followd by (3) acid pickling where the parts are immersed into a hot sulfuric acid solution. Pickling removes all mill scale and rust, which might have remained on the surface. The last chemical step before galvanizing is (5) fluxing. The steel material is dipped into an aqueous solution of zinc ammonium chloride. This removes all oxides from the surface and supports bonding of the zinc to the steel surface. Between the single steps the components are (2, 4) washed (rinsing) to avoid contamination of the following bath.
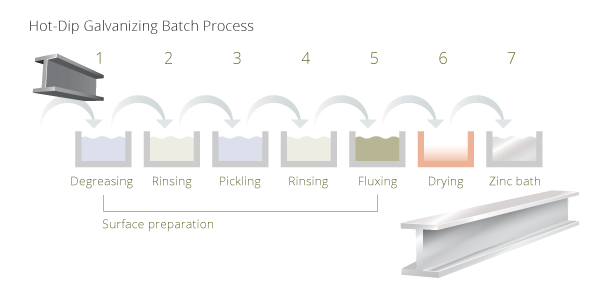
Copyright © 2025 build-your-vision.eu; without any guarantee or liability
Today the batch galvanizing industry is highly automated. Large-scale immersion facilities allow galvanizing of massive steel beams as well as the processing of smaller parts. Smaller items are frequently galvanized using perforated baskets. After the zinc bath the baskets are centrifuged to remove excess zinc. Large-scale facilities can reach dimensions up to 12-18 m in length in the galvanizing kettle.
The basic specification for hot dip galvanized coatings on iron and steel articles is defined by EN ISO 1461 ‘Hot dip galvanized coatings on iron and steel articles – specifications and test methods’.
Continuous Hot-Dip Coating
The process is optimized for high speed galvanizing which means the complete pretreatment process, the galvanizing process, and the cooling process are integrated in one production line. Production line speed up to 180m/min is achievable with a capacitiy up to 700.000 tons per year. On www.galvanizeit.org the process is described as follows: "Preparing the steel for the continuous galvanized coating begins with cleaning in an alkaline liquid combined with brushing, rinsing, and drying. Then the steel passes into the heating or annealing furnace to soften it and impart the desired strength and formability. In this annealing furnace, the steel is maintained under a reducing gas atmosphere, composed of hydrogen and nitrogen, to remove any oxide that may be on the surface. Just as in the batch hot-dip process, the steel must be completely clean of oxides and contaminants for a successful coating. As the steel exits the furnace, it enters into a vacuum chamber, or snout, before entering the molten zinc bath to prevent and air from reoxidizing the heated steel product. The steel is then sent around a submerged roll in the molten bath to create the bonded coating and removed in a vertical direction. As the product is withdrawn from the bath, precisely regulated, high-pressure air (air knife) is used to remove any excess zinc to create a closely controlled coating thickness. The steel is then allowed to cool and solidify before contacting another roll to avoid transferring or damaging the coating."
The basic specification for continuously hot galvanized steel is defined by EN 10346:2015 'Continuously hot-dip coated steel flat products for cold forming - Technical delivery conditions’.
Image of a continuouse coil galvanizing line ... coming soon.
Galvannealed Coating
Galvannealed coating for coil coating is primarily a modified production process of the continuous hot-dip galvanized steel production. After the hot-dip zinc bath the coil sheet is exposed to a heat treatment causing iron and zinc layers to diffuse into one another which results in a zinc-iron alloy layer at the surface of the sheet. The diffusion process starts at around 500 to 560°C. About 10 percent iron diffuses into the zinc layer (there are many parameters influencing the process like temperature, annealing time, steel grade, Formular of the zinc pot) with a thickness of approximately 10 µm. The zinc-iron alloy on the sheet is more brittle and hardener caused by the presence of the iron. Some amount of powdering can appear when the metal is formed.
Galvanealed steel sheets have an exceptionally uniform surface well suited for painting directly onto its surface. Typical uses include office furniture, commercial refrigerators and freezers, door frames, and predominantly for the automobile industry.
Electrogalvanizing
The main differences between hot-dip galvanizing and electrogalvanizing is that the zinc layer from the hot-dip process is almost always several times thicker than it is created by electrogalvanizing. There are of course some more differences.
For the electrogalvanizing process the steel is immersed in/guided through an acid electrolyte bath, and electricity is used to move electrons from the anode to the cathode, which includes the zinc anodes to be oxidized and dissolve as zinc ions in the solution, be transported as ions through the solution, and be reduced as metal onto the workpiece (cathode). The process is called electrodeposition. The rate at which the anode is dissolved is equal to the rate at which the cathode is coated. There are other techniques which use a non-consumable anode such as lead or carbon. In this case the solution, which holds the ions to be plated must be periodically replenished as they are drawn out of the solution. Titanium clad and solid titanium anodes for electrogalvanizing cells seems to be state-of-the-art for stable anodes.
The basic specifications are defined by DIN EN 10152:2009-07: Electrolytically zinc coated cold rolled steel flat products for cold forming - Technical delivery conditions;
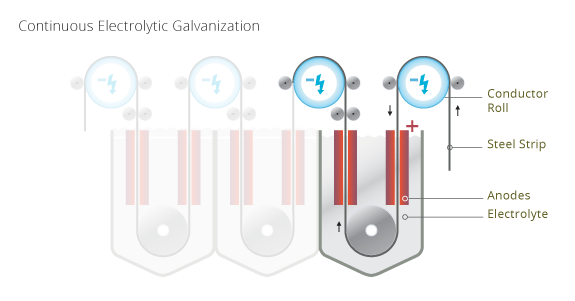
Copyright © 2025 build-your-vision.eu; without any guarantee or liability
Sherardizing (Dry Galvanization)
Sherardizing is a common used process for galvanizing metal surfaces through a thermo-diffusion process. On wikipedia it is explained: "Sherardizing is a process of galvanization of ferrous metal surfaces, also called vapour galvanising and dry galvanizing. The process is named after the British metallurgist Sherard Osborn Cowper-Coles (son of naval inventor Cowper Phipps Coles) who invented and patented the method ca. 1900. This process involves heating the steel parts up to ca. 500°C in a closed rotating drum that also contains metallic zinc dust and possibly an inert filler, such as sand. At temperatures above 300°C, zinc evaporates and diffuses into the steel substrate forming diffusion bonded Zn-Fe-phases." (Other information say, sand is no more used.)
The process is used for many metal products such as steel, stainless steel, castings, and forgings. Sherardized products have a matte grey metallic appearance which acts as a perfect primer for topcoats. The final surface is sacrificial and offers very high galvanic protection to the steel/metal parts. Some of the main advantages are that the process is non-toxic, free of heavy metals, it has almost no discharges to the environment, and additional an extremely low water consumption - a critical issue for the galvanizing industry. Sherardizing suits perfectly for small metal parts like springs, nails, screws, nuts and bolts, chain link. Especially for components used in aggressive salt water atmosphere sherardized parts are long-lasting and contiune to function.
The process is internationally specified in DIN EN ISO 17668 and EN 13811 Sherardizing/Zinc diffusion coatings.
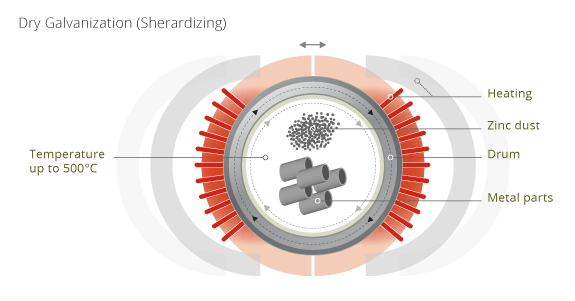
The sourrounding heater can be opended to exchange the drum.
Copyright © 2025 build-your-vision.eu; without any guarantee or liability